Via our overseas network and agreements, Green Technology of Power provides an industry leading component inspection, repair and overhaul service, over the complete range of equipment serviced. Perform many Component Repair operations; protective coatings are applied to both the internal and external components in order to minimize the detrimental effects of corrosion and erosion.
The paints can be classified as a member of aluminium based corrosion resistant paints, stoving enamel grey, and dry film lubricants. A list of some of the paints that can be applied include PL101, PL163, PL165, PL205, PL237, PL239, Xylan 1010 (Teflon), Molykote D321R, Sermatel 570A, Sermatel 709, and Sermatel W. However, other coatings have been applied upon customer request.
In addition to masking, painting and curing operations, other capabilities of the Component Repair department include blending and polishing, TIG welding and glass bead blasting.
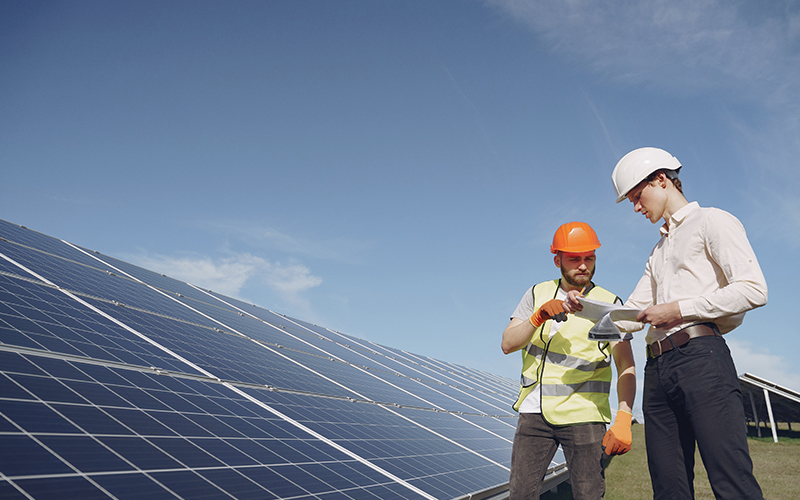
We carry out numerous types of component overhaul to OEM specifications, but have also our vendor developed advanced repairs and coatings which improve turbine performance and extend service life. These tested and validated advanced repairs, allow us to salvage components which would otherwise be replaced with costly new ones.
- Advanced Repairs Development
- Ultrasonic and pyrolytic cleaning
- Specialized surface treatment and coatings
- HVOF and Plasma applied coatings
- Vacuum brazing and Heat Treatment
- Electron Beam / Laser welding
- 6 Axis CNC Automated Electro discharge and wire machining
- Complete NDT capabilities including 3D Digital x-ray
- Positive Material Identification (PMI) Scanning
- Fully automated 7 axis precision CNC machining
Air Filtration Custom Solutions
In many industrial processes and whenever safety is required, the filtration of air and liquids is indispensable. Filtration impacts the quality of an end product, the productivity of a company and its contribution to environmental protection. This is why companies expect a great deal from filtration. This is why our customers expect a great deal from us.
In many industrial processes and whenever safety is required, the filtration of air and liquids is indispensable. Filtration impacts the quality of an end product, the productivity of a company and its contribution to environmental protection. This is why companies expect a great deal from filtration. This is why our customers expect a great deal from us.
Gas Turbine Air Filters
The Performance Upgrade For Gas Turbines
Our vendor has supplied GT air filters to the power generation industry since the mid 1980's. Whether your plant is a peaker or a base-load station, we can upgrade your gas turbines' performance with expertly engineered systems made up of our coalescers, pocket filters, filter cells, (H)EPA filters and other high-performance components.
Inlet air quality is a make-or-break factor for gas turbine performance. Intake of particulate-laden air into a gas turbine causes fluctuations in power output, resulting in headaches for power plant operators.
90% of power capacity loss of gas turbines is due to inadequate filtration of inlet air.
Inlet air quality is a make-or-break factor for gas turbine performance. Intake of particulate-laden air into a gas turbine causes fluctuations in power output and resultant headaches for power plant operators.
The underlying cause of the problem is compressor fouling. In such cases operators often look to on-line compressor washing as a quick fix to restore power and efficiency. The success of this measure is short lived as on-line cleaning simply washes contaminants from the front blades to the inner blades of the turbine. Shutdown of the turbine permits much more effective washing but causes costly downtime. In any event, the capacity loss comes back again due to the ongoing contamination which continues to build up and damage blades and other components.
Air Intake Filtration Survey
Green Technology of power have a well-trained certified level measurement engineers with experience of Gas Turbines more than 20(Twenty) Years working the Power plant and Oil & Gas sectors. Air intake filtration survey means the following:
-
Evaluation of the old filter system
Measurement and evaluation of the existing filtration system and installing of the new filters. Data recording of new filter element of each stage to make a reference measurement. Ambient air, clean air, measurement at different filtration stages of the following:
- Particle counting
- Pressure drop
- Temperature
- Dew point
- Relative humidity
- Velocity
-
Evaluation of the new installed filter system
Removing of the new filters after 3 month operation and sending to our overseas laboratory analysis with the data recording formulary. Sending report and comments
-
Reporting and final results
Evaluation of the results, reporting and recommendations.
-
Methods
Identifying of 4 filters in each filter wall per each gas turbine by installing new filters:
- Identifying of 4 filters in each stage by number (Each filter element)
- Weighting (Each filter element)
- Establishment of an installation drawing of the filter elements
- After 3 month or 2000 fired hours, removing 1(one) filter element per stage per gas turbine, weighting, packing in a plastic bag, filling up the recording formulary and sending in a cardboard box to our overseas laboratory for analysis.
Installing measurement equipment:- Particle counting
- Pressure drop
- Temperature
- Dew point
- Relative humidity
- Velocity
Targets
Identifying the filtration problems as soon as possible to avoid any hot corrosion damages on the hot gas parts and reduce the maintenance costs Optimize the filtration system, pressure drop
Laboratory Filter Analysis In Conformity With latest EN779/2012 and ISO.
- Free dust weighting and evaluation
- Filter pressure drop, efficiency measurements
- Dust kept into filter extraction by shaking and analysis
- Dust extraction by water and analysis
- Filter media analysis after water extraction